top of page
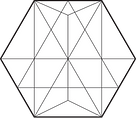
JR
JEFFERSON ROOFING
COMMERCIAL | RESIDENTIAL | LUXURY
ROOFERS IN NAPA, ROOF BUILDERS, ROOFING, ROOF EXPERTS, ROOF REPAIR, SONOMA, FIX MY ROOF, JEFFERSON ROOFING
SHAKE ROOFING
A shake is a basic wooden shingle that is made from split logs. Shakes have traditionally been used for roofing and siding applications around the world. Higher grade shakes are typically used for roofing purposes, while the lower grades are used for siding purposes. In either situation, properly installed shakes provide long lasting weather protection and a rustic aesthetic, though they require more maintenance than some other more modern weatherproofing systems.The term shake is sometimes used as a colloquialism for all wood shingles, though shingles are sawn rather than split.
In North America shakes are typically made from California redwood (Sequoia sempervirens) and Western Red Cedar (Thuja plicata), while in Scandinavia and Central Europe they are more commonly made from pine (Pinus sylvestris).
There are various types of shakes, the main differentiating feature between shakes and other types of shingles is that shakes are splitwhile most shingles are sawn on all sides. The sizes also vary from country to country; in North America shakes are usually made in 24-inch lengths - the most common, 18-inch barn shake, or even 48-inch shakes, which are typically used for siding. In Scandinavia shakes, traditionally used only for roofing, are generally smaller than in North America, measuring 13-16 inches long, 4-6 inches wide and 1/8 thick.[1] Likewise wooden shingles are manufactured in differing lengths, in North America, 16-inch, 18-inch and 24 inches.
Shake blocks are split into 1 inch thick slats called blanks, using either a hydraulic press with a blade attached, called a cuber, or split by hand using a froe and mallet. These blanks are uniform in thickness throughout if split from the same edge without flipping the block. Alternatively, the splitter may flip the block after a blank is taken off each edge, which results in a tapered split from end to end, called tapers or hand-split.
The blanks which are not tapered require further processing before application to create this taper, and are run through a large band saw, pushed by hand to cut them from corner to corner forming a tapered shake, sawn on one face.Shingles are cut from the blocks using a circular saw, typically 42-48 inches in diameter. The blocks are clamped in a carriage which slides back and forth across the blade, tilting and moving the block closer to the blade with each pass to automatically form a tapered cut of the correct thickness. The edges of the shingle are then cut with another circular saw called a "trim saw", to remove irregular edges. The result is a tapered shingle sawn on all six sides.
The thickness of the butt, or thicker end of the tapered cut, is usually 3/8 inch thick, but is also commonly made to be 5/8 inch, and can be made to any custom specifications.
bottom of page